
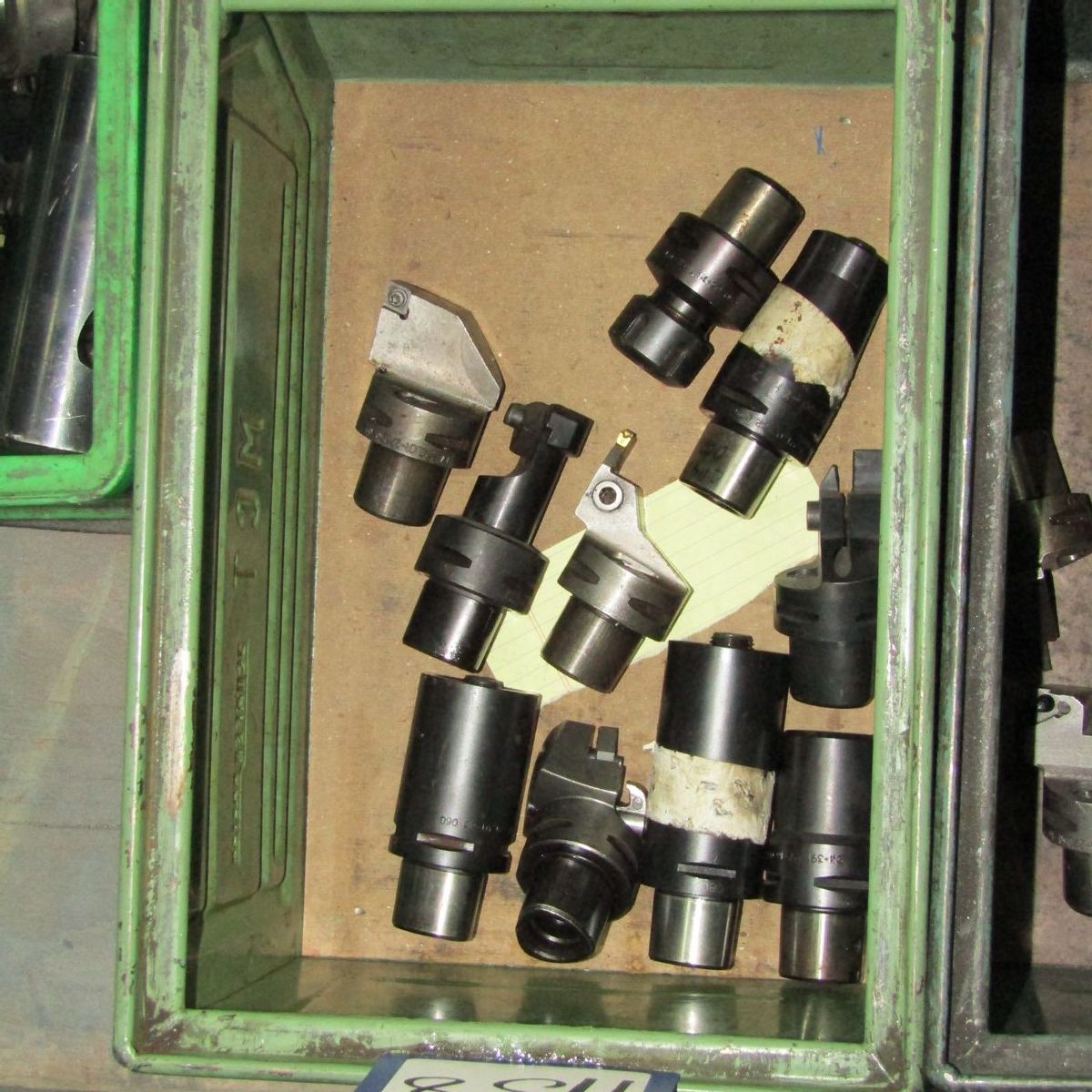
For instance, the capto tool holders selection includes models that are designed to attach to CNC lathes and milling stations, making it easy to swap in different parts to smooth the production process. You can manage tasks easily and know exactly where everything is whenever you need it.Īt, you'll find a massive selection of tool holder products, with standalone holders and products designed for specific situations. It allows you to have the components and tools you need close to hand so that you can switch between hammers, screwdrivers, wrenches and the tools you rely on. A tool holder like that is more than an accessory. That's where a capto tool holders could come in really handy. Even in fine machining, where high spindle speed is required, existing MCs can be operated with the speed-increasing spindles.Organization is everything in workshops, whether you are fixing things at home or working in a complex industrial operation. It is attached to the main spindle of an existing MC to increase the spindle speed. The speed-increasing spindle is also a tool holder that boosts spindle performance. As a result, by effectively utilizing the angle head, various machining operations can be performed with only one attachment of the workpiece to the table, improving machining efficiency. The angle head is a tool holder that changes the machining direction of the tool to a specific angle, which allows machining with one new axis added to the existing MC. One of the tool holders that increase the functionality of the MC’s main spindle is angle head. In addition to the three tool holders introduced above, there are many other types of tool holders for MC, such as arbors for attaching indexable milling tools, drill chucks for holding drills, tool holders used for tapping, boring bars for boring, etc. The BBT shank can also be used interchangeably with the BT shank, making it easy to use. Because the two surfaces are in close contact, the BBT shank is more rigid than the BT shank, and vibration during machining can be controlled.

On the other hand, with a BBT shank, the shank end face and main spindle end face are in close contact, so the shank is not pulled into the spindle bore and machining can be performed with high accuracy even at high spindle speeds. In this case, when the spindle rotates at high speed, the main spindle bore expands due to centrifugal force, causing the shank to be pulled into the spindle bore, which changes the position of the tool and may negatively affect machining accuracy, especially in the Z axis. With the BT shank, only the tapered part is in close contact with the main spindle, and there is a gap between the shank end face and the end face of the main spindle. “Dual contact” means that shank contact the spindle taper and spindle face simultaneously.
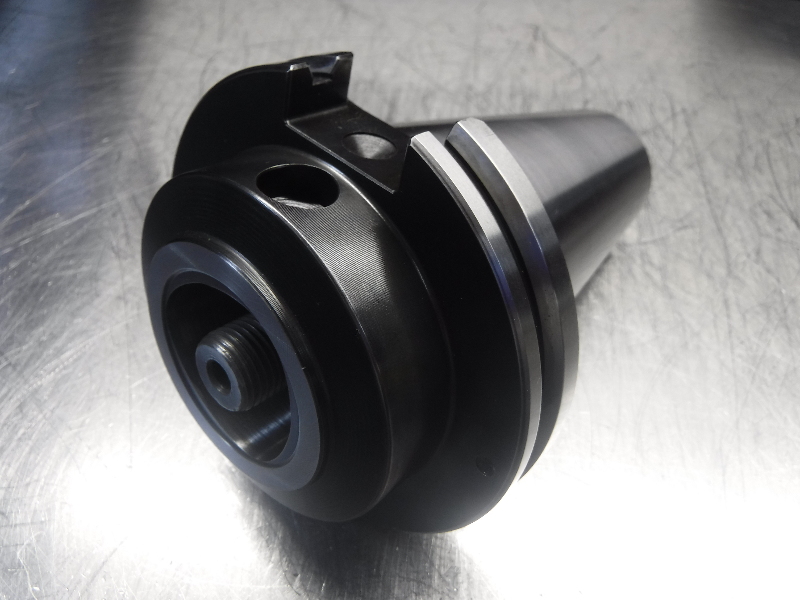
It is difficult to distinguish the BBT shank from the BT shank at first sight, but the biggest difference is that BBT shanks are dual contact spindle system. BBT shank is a standard developed independently by BIG DAISHOWA SEIKI, a Japanese leading tool holder manufacturer.
